

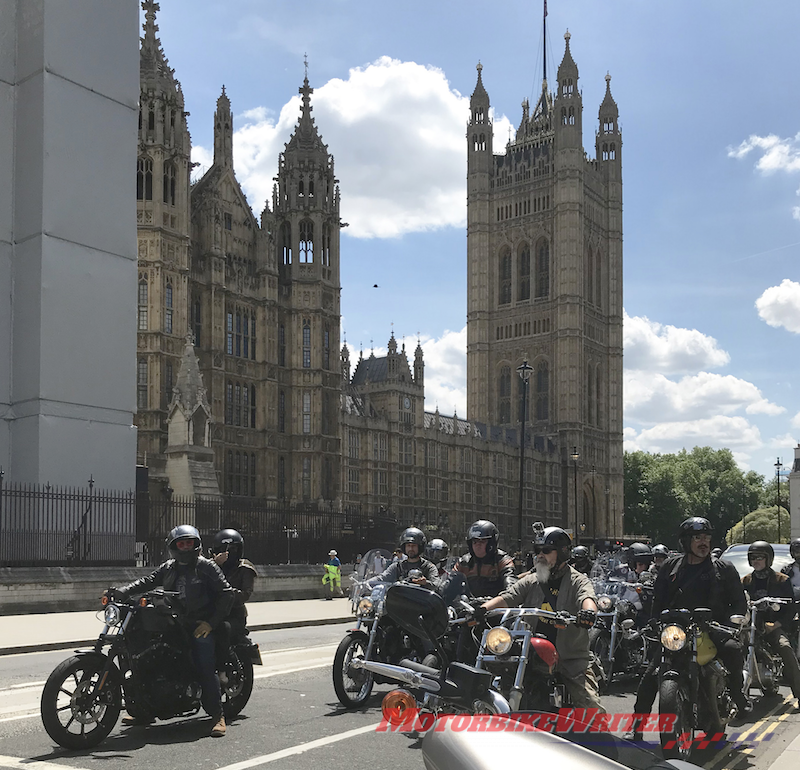
By using it, you can keep the heat low (the base metals don't actually melt), and thereby minimize any distortion in the sheet metal. Also note the use of silicon bronze filler rod. By using dissimilar metals, you can avoid this all together. Then, when you try to remove the bolts, the stainless will instantly gall and you won't get the two apart. If you use stainless bolts and stainless nuts, the heat from the weld will cause them to fuse together just a tiny bit.
CUSTOM MOTORCYCLE PLATES VICTORIA LICENSE
Using an old license plate as a template, I bolted it to the bracket and tacked the nuts with the TIG welder. If you're not confident, hex nuts look good too! Use caution when using this technique, as it can be dangerous for the inexperienced. Then, grip the all-thread in a drill and spin it as you apply it to a grinding wheel, sanding disc, or sanding belt. Simply stack the nuts on short piece of all-thread and tighten together. You can grind them round as well if you don't have a lathe. Thus, I threaded four 1/4-20 hex nuts onto a piece of all-thread, then turned them round on a lathe. While nuts and bolts would have worked fine, I wanted a cleaner, more permanent solution. While not perfect solution, the flathead screws now sit much closer to the surface of the bracket, and no longer interfere with the license plate.
CUSTOM MOTORCYCLE PLATES VICTORIA DRIVER
Using an impact driver (Milwaukee M12), I tightened the screw into the round bar whilst I head onto the bracket with a gloved hand. I first applied a bit of grease on the threads and tapered surface of a flat head screw, then I gripped the round bar in a vice, passed the flat head screw through the 1/4" hole drilled in the bracket, and threaded the screw into the round bar. I quickly drilled, tapped and countersunk a piece of steel 1/2" round bar. The flaring die can be used in a vice, an arbor press a hydraulic press or even a largish C-clamp.Īfter flaring the larger holes, I realized the screws that secure the bracket to the rear fender would interfere with the license plate lying flat on the bracket.
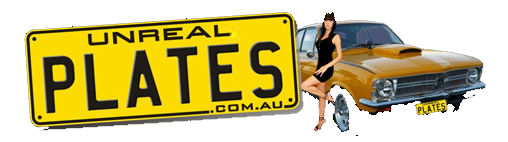
I've flared both mild steel and aluminum, perhaps 100 holes and it shows no wear. It's made from 4140 steel, and is not heat treated. It's designed for 3/4" holes, though it may work on other sizes. You can deburr the backside of the hole (which almost always has a gnarly burr) with the same bit, just go slow.ĭepending on who you ask, these dies are called either dimple dies or flaring dies. Plus, they have the added benefit of putting a sweet chamfer on the hole. They are much safer, especially when drilling larger holes, as they have less propensity to grab and spin the part you're working on. When drilling a hole in sheet metal greater than ø1/4", I prefer to use a step-bit, or as my friend Conor calls them, a "christmas-tree-bit". After I was pleased with the sketch, I measured the holes accurately, and drilled the holes. I also roughly sketched where the mounting holes for the bracket would go, and where the lightening (Speed®) holes would go. Then, I traced the holes using a Sharpie®. I cut the sheet steel slightly wider than the license plate, and the same height. Nevertheless, it's plenty sturdy for a license plate. Though I ended up folding the short edges, in retrospect, it would have been better to fold the long edges. I used a bit of 16 gauge I had lying around. I knew I wanted something simple, stylish and lightweight. I didn't want to spend much in terms of time, effort of cash.
